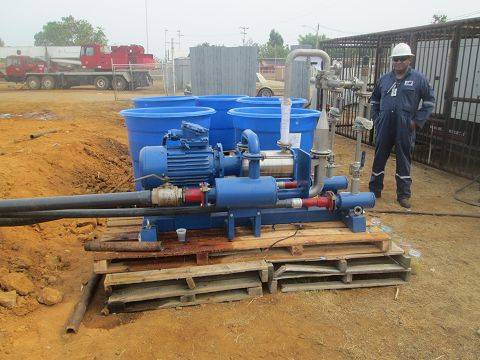
Hydrodynamic cavitation is a process of generation of cavities (bubbles) filled with gas and vapor dissolved in fluid. The cavities appear when fluid flows around obstacles or vice versa, the obstacles (blades) move in liquid.
The cavities explode into tiny bubbles, which can burst under certain conditions. The burst bubbles release local pressure up to 103 Pa, with subsequent jet formation 700 – 800 m / s and local energy generated at 10 kW / m3.
Cavitation destroys everything, no material can resist it. Therefore, the processes of dispersion, emulsification, activation, crushing, separation, mixing, energy production, intensification of technological processes are performed with minimum energy.
Cavitation devices are based on the processes of hydrodynamic cavitation, effective mixing, activation, dispersing and homogenization. They are new generation equipment greatly intensifying and accelerating the processes in liquid environments, significantly lowering the cost of energy and resources.
These devices can be classified according to operation mode, input and output of the gas phase, the type of design and features, and the types of cavitation process, which could be natural and artificial. Natural cavitation occurs in liquids when pressure falls below vapor pressure. It creates cavities and cavitation bubbles in liquid filled with steam and diffused gases.
Natural cavitation is characterized by two phases: initial bubble cavitation and oscillation of bubbles.
Bubble cavitation has a cavitation field with a low pressure zone, filled with cavitation bubbles in clusters, and a high pressure zone, where cavitation bubbles are broken to form a micro-flow at 50-1500 m / s and the pressure of 102 MPa.
The bubbles oscillate and grow slowly in size or shape, larger than the cavitator by 1-5 times or more. The pressure pulse produces a periodic growth and collapse of cavitation bubbles. The bubble oscillation mode is widely used in the processes of mixing, degassing, evaporation and contact heating.
Artificial cavitation occurs by venting liquid flow with gas. The gas is generated under pressure.
Artificial cavitation is characterized by two types of gas-leakage: the pulsating or portion-leakage, and the constant gas-leakage with continuous gas flow. Artificial cavitation mode is used for the aeration of sewage, for mixing gas and liquid, for contact heat transfer, flotation, it is also used in ejection equipment.
In natural cavitation the pressure in the cavity is equal to the vapor pressure of the liquid at the constant liquid temperature. In artificial cavitation the pressure is formed in the cavity due to the enhanced gas-leakage. It is always higher than the vapor pressure. This allows to simulate a wide range of cavitation, for example, increasing the flow of liquid would cause cavitation on the walls of the cavity.